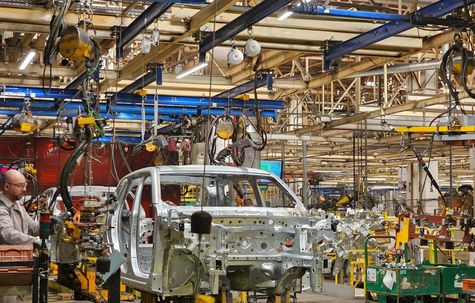
REPORTAJ: Am fost acasă la Dacia și am văzut cum este asamblat noul Bigster
După o pauză de aproximativ doi ani, uzina Dacia de la Mioveni și-a deschis porțile pentru jurnaliști. Momentul a coincis cu intrarea primelor exemplare Bigster pe linia de asamblare.
În toamna anului trecut, Dacia ne-a invitat să vedem, pentru prima oară, noul Bigster: un SUV prin intermediul căruia, constructorul de la Mioveni își anunță intrarea în segmentul C, cel mai profitabil segment auto de pe Bătrânul Continent.
Dar Bigster este mai mult de atât. Vorbim despre cea mai mare Dacia produsă vreodată, având în vedere că este cu 23 de centimetri mai lungă decât Duster. Apoi, este cel mai tehnologizat model din istoria mărcii, unul care a introdus mai multe premiere: plafon panoramic și hayon acționat electric, ca să dăm doar două exemplare.
Apoi, Bigster Hybrid este cea mai puternică Dacia din istorie (de serie, desigur). Ascunde sub capotă un sistem de propulsie hibrid, fără încărcare la priză, care oferă 155 de cai putere și care are la bază un motor de 1.8 litri, aspirat natural. Acesta din urmă are mai multe legături cu țara noastră decât ai crede, dar despre asta îți spun mai încolo.
Povestea a continuat apoi cu testele internaționale, la care Automarket a luat parte în urmă cu două săptămâni. Embargoul pe impresiile de condus expiră chiar mâine, așa că fii pe fază pentru că urmează un articol în care îți spunem cum se simte de la volan noul Bigster.
Pentru ca tabloul să fie complet, Dacia a deschis porțile uzinei de la Mioveni, după o pauză de aproximativ doi ani, astfel că am avut ocazia să vedem cum sunt asamblate primele exemplare Bigster. Mai mult, am aflat că ele vor ajunge în showroom-urile din toată țară începând cu data de 10 aprilie. Comenzile au fost deja deschise.
Cu acest prilej am mai aflat câteva informații proaspete. De pildă, în România s-a depășit deja pragul de 1.200 de comenzi, iar în Europa au fost înregistrate deja peste 10.000. Peste 90% dintre clienți au optat pentru un nivel de echipare de top, adică Extreme sau Journey, iar două treimi au comandat motorizarea hibrid.
Așa cum era de așteptat, noua culoare exterioară, Albastru Indigo, este în topul preferințelor.
Revenind, însă, la vizita uzinei de la Mioveni, reprezentanții companiei ne-au pregătit un tur prin trei departamente: Presaj, Caroserie și Montaj General. Aici am văzut cum modelele Dacia, adică Bigster, Duster, Logan, Sandero (da, încă se produce aici, dar pentru piața locală) și Jogger evoluează de la o simplă coală de tablă, la o mașină perfect funcțională.
Înainte să trecem mai departe și să îți descriem puțin procesul de producție, trebuie să ne oprim pentru a vorbi, pe scurt, despre istoria uzinei de la Mioveni. Epicentrul industriei auto din România, dacă îmi permiți această formulare.
UZINA AUTO DE LA MIOVENI. SCURTĂ ISTORIE
Deși în ziua de azi poate rivaliza cu uzinele unor constructori de automobile consacrați, din punct de vedere al calității muncii și, desigur, al tehnologiei, fabrica de la Mioveni a avut începuturi modeste. După investiții de sute de milioane de euro, realizate de-a lungul anilor, fabrica Dacia este acum legată prin autostradă cu Bucureștiul și, mai departe, de portul Constanța.
În câțiva ani, sperăm noi nu prea mulți, va fi conectată printr-o șosea de mare viteză și cu granița de vest a României, pentru ca mașinile să poată fi livrate mai ușor și mai repede către țările din Occident.
Așadar, povestea uzinei de la Mioveni începe în anii '60. Pentru a scurta drumul de la proiectarea unui automobil și lansarea lui în producția de serie, autoritățile române au luat decizia să producă o mașină sub licență, obținută de la un producător străin.
S-au înscris mărci ca Renault, Peugeot, Fiat, Alfa Romeo și Austin, însă francezii de la Renault au avut câștig de cauză. Inițial, Renault voia să le permită românilor să producă, sub licență, modelul Renault 12, dar, din motive tehnice și economice, oferta a fost retrasă.
Având în vedere că cele două părți semnaseră deja contractul, Renault le-a permis românilor să înceapă asamblarea anticipată a unui model intermediar. Este vorba despre Renault 8.
Marca Dacia a luat ființă în 1966, la Colibași (Mioveniul de azi). Tot în 1966 începe construcția Uzinei de Autoturisme Mioveni, care s-a încheiat într-un timp record, de doar un an și jumătate. În data de 1 iulie 1968, încep testele la cele 217 stații de lucru din uzină, iar în august se testează primul motor.
Uzina a fost deschisă, oficial, în luna august 1968 și, tot atunci, începe producția modelului Dacia 1100. Dăm pe repede înainte până în 1999, atunci când destinul mărcii românești avea să se schimbe definitiv. Renault achiziționează 51% din capitalul Dacia, iar la mijlocul anului 2000 este lansat primul model din noua eră: Supernova.
O evoluție a modelului Dacia Nova, Supernova era echipat cu un sistem de propulsie de 1.4 litri MPI, furnizat de Renault.
Așa cum spuneam, au urmat apoi investiții în modernizarea uzinei. În prezent, fabrica Dacia de la Mioveni are o suprafață totală de 355.000 de metri pătrați și o cadență de 65 de vehicule/oră, sau 1.357 de vehicule pe zi. Aici lucrează aproape 6.900 de angajați.
Uzina de la Mioveni exportă mașini în 71 de țări, în mare marte din Europa. De fapt, 90% din producție merge către export. Dacă tot suntem la capitolul procentaje, peste 90% din producție este reprezentată de modelele Duster și Bigster, iar restul de Sandero, Logan și Jogger.
Integrarea unui model ca Bigster pe linia de asamblare nu a fost o treabă simplă și a fost nevoie de o investiție care s-a ridicat la 340 de milioane de euro.
PRIMA OPRIRE: DEPARTAMENTUL PRESAJ
În faza incipientă, orice mașină este o bucată de tablă nefinisată. Primii pași sunt făcuți în departamentul Presaj. Această secție se află în primele două locuri în clasamentul uzinelor din Grupul Renault și prelucrează 800 de tone de tablă în fiecare zi.
Materia primă este importată din Europa, inclusiv din Italia.
În departamentul presaj lucrează circa 400 de oameni, iar pentru producerea modelelor Duster și Bigster a fost necesară o investiție de 36 de milioane de euro.
Fâșiile de tablă brută sunt preluate și sunt transportate către linia de prese. Este vorba despre o linie nouă, robotizată, formată din 4 prese, cu o cadență de 55 de bătăi pe minut.
Presele utilizate aici au o forță cuprinsă între 400 și 2.400 de tone, pe care o poți simți până în cele mai mici celule dacă stai câteva secunde lângă o asemenea mașinărie.
Aceste prese formează primele panouri, iar, la finalul liniei, piesele rezultate sunt controlate de 10-14 operatori. Acest proces nu este, încă, automatizat, dar reprezentanții Dacia susțin că proiectul este pregătit și ar costa 5.5 milioane de euro. La momentul oportun, spun ei, proiectul de automatizare va fi implementat.
A DOUA OPRIRE: DEPARTAMENTUL DE CAROSERII
A doua oprire din turul nostru la uzina Dacia de la Mioveni a fost în departamentul de Caroserii, acolo unde procentajul de roboți utilizați în procesul de producție este mult mai mare decât în departamentul Presaj.
În total, la Caroserii există 550 de roboți Kuka și ABB. Sunt aceeași pe care îi regăsești prin mai toate uzinele auto din lume. Ca să îți faci o idee despre cât s-a modernizat fabrica română, în 2005-2006, departamentul Caroserii era robotizat în procentaj de doar 5%.
În acest departament, în care lucrează 1.400 de persoane, vin piesele de la Presaj, se sudează și la final ai o caroserie. Trebuie spus că 60% din punctele de sudură sunt realizate automat, deci de roboți, iar restul manual.
Linia de fabricație pentru Duster și Bigster este identică și este realizată sub forma literei U. Primele care intră pe linie sunt cele 3 componente importante ale mașinii, inclusiv partea frontală. Apoi se sudează părțile laterale.
Pe partea opusă, caroseria are deja 80% din componente. Lipsesc elementele detașabile, cum ar fi aripile, portierele și așa mai departe. Ele vor fi alipite ulterior.
Linia poate fabrica 40 de mașini pe oră sau, cu alte cuvinte, 900 de caroserii pe zi. La linia de Carosaj, caroseriile stau circa 2 ore și jumătate.
Spuneam că "greul" cade pe roboți. Ei au propriile sisteme de monitorizare, dar sunt urmăriți și video, pentru a se asigura că totul decurge normal.
Urmează apoi gravarea seriei de șasiu, sau numărul VIN dacă vrei, iar din acest moment caroseria primește o identitate unică și poate fi urmărită prin intermediul sistemului informatic. De aici și până la departamentul de Montaj General, caroseria face în jur de 10-11 ore și trece, desigur, și pe la vopsitorie.
A TREIA OPRIRE: DEPARTAMENTUL MONTAJ GENERAL
Noi am sărit peste departamentul de vopsitorie, dar reprezentanții fabricii ne-au spus că uzina de la Mioveni a fost printre primele care au utilizat vopsele pe bază de apă.
Așadar, a urmat departamentul Montaj General, acolo unde mașina nu mai este doar o caroserie goală. Ea ajunge aici gata vopsită, iar 1.800 de persoane așteaptă să o transforme într-o mașină perfect funcțională. Primul lucru pe care îl fac este să demonteze portierele, pentru un acces cât mai facil.
Pe lângă cei 1.800 de angajați, în cel mai mare departament al uzinei "lucrează" și 270 de AGV-uri, adică roboți autonomi care transportă piesele între stații.
Linia de Montaj are o lungime de 1.2 kilometri și o capacitate de 170 de vehicule pe oră. La fiecare 55 de secunde iese câte un vehicul de pe această linie.
Pe această linie se montează toate componentele mașinii, inclusiv motorul și cutia de viteze. După montarea sistemului de propulsie, piesele rămân imobilizate timp de 10 ore, după care vin strânse. La final, se fac ultimele reglaje și teste, înainte ca mașina să iasă de pe linia de asamblare.
Departamentul Montaj are o integrare locală a pieselor de 50-55%. Circa 65-70% dintre componente sunt comune pentru modelele Duster și Bigster.
VIZITĂ LA HORSE ROMÂNIA
Turul nostru s-a încheiat cu o vizită la cei de la Horse România. Deși se regăsesc pe platforma de la Mioveni, ei sunt o entitate separată, cu buget propriu și cu propria strategie tehnologică.
Anul trecut, Renault a înființat oficial, împreună cu chinezii de la Geely și ulterior cu cei de la Aramco, compania Horse Powertrain Solutions, o divizie nouă de motoare termice eficiente.
La nivel global, Horse are peste 9.000 de angajați, 11 fabrici de producție, activează în 7 țări (Brazilia, Chile, Argentina, Spania, Turcia, România și Portugalia) și are venituri de peste 7.6 miliarde de euro.
Horse România are în prezent puțin peste 2.700 de angajați la București, Titu (centru tehnic pentru software și implementare) și, desigur, la Mioveni. Această entitate separată are o turnătorie de aluminiu unde prelucrează 90 de tone de metal în fiecare zi, produce cutii de viteze (o cutie la fiecare 30 de secunde) și motoare (un motor la fiecare 45 de secunde).
Anual, Horse România are o capacitate de producție de 450.000 de motoare (45% merg către Dacia) și 670.000 de cutii de viteze.
Printre "clienții" sai sunt uzinele Dacia de la Mioveni și Tanger (Maroc), fabricile Renault din Bursa, Novo Mesto, Maubeuge, Curitiba și Medellin, dar și uzina Nissan din Sunderland.
La Mioveni, Horse produce motoarele HR10 și HR12 (1.2 litri, 3 cilindri), ambele fiind regăsite atât pe modele Renault cât și Dacia.
MOTORUL DE PE BIGSTER HYBRID, DEZVOLTAT ÎN ROMÂNIA
Ce nu știe multă lume, din păcate, este că motorul HR18, cel care stă la baza noului sistem de propulsie hibrid disponibil pe Bigster, este dezvoltat în România încă din faza de concept. Unitatea pe benzină (o evoluție a motorului de 1.6 litri de pe Duster Hybrid) are 1.8 litri, injecție directă și un raport de compresie de 14:1.
Propulsorul funcționează în ciclu Atkinson și are o eficiență de 40.5% (38.1% are HR16). Este atașat la o transmisie multimodală, așa cum bine știi, care are codul intern DB45. Generația anterioară avea numele de cod DB35. Noua transmisie a fost optimizată pentru a reduce zgomotul și pentru a asigura o livrare mai fluidă a puterii.
De asemenea, noul sistem hibrid de pe Bigster are o baterie mai mare, de 1.4 kWh (și ea dezvoltată la noi în țară, la fel ca transmisia și motorul).
Nu în ultimul rând, motorul HR18 promite o reducere a emisiilor de CO2 cu circa 7 grame/km și reprize de accelerație mai bune (un câștig de 1 secunde pentru 0-100 km/h și 1.5 secunde pentru 80-120 km/h, față de motorul de 1.6 litri). Totodată, capacitatea de remorcare a crescut de la 750 la 1.250 de kilograme.
Deși a fost gândit în România, motorul se produce în Spania și la Bursa, în Turcia.
Mai trebuie spus că noua generație de motoare Horse sunt proiectate pentru a funcționa cu combustibili sintetici, de aici și aportul Aramco la această entitate.
De pe linia de asamblare de la Horse România ies zilnic 1.650 de motoare. După instalarea tuturor componentelor, inginerii realizează un test la rece, unde calculează toți parametrii, iar mai apoi urmează un test la cald, cu ulei în motor. Acest test la cald include și un test de pornire.
În acest departament sunt și câțiva roboți, care realizează testele de etanșeitate.
Ca o concluzie, uzina Dacia de la Mioveni a trecut prin transformări majore în ultimii aproape 60 de ani. În prezent, este o fabrică modernă care asamblează cel mai tehnologizat model al mărcii: Bigster. El nu doar că a fost desenat în România, dar motorul care stă la baza celei mai puternice versiuni a fost, de asemenea, gândit în țara noastră.
Iar acestea sunt doar două lucruri cu care ne putem mândri. Desigur, fără aportul francezilor de la Renault, drumul Dacia ar fi fost cu totul altul.
Deja de la primele fraze am sesizat o "mica" greseala, mai exact este mai mare cu 23 de cm , nu 23 de milimetri.